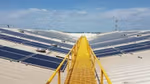
Unilever solar electricity deal powers renewable energy use in India
We’re partnering with our collaborative manufacturers in India to tackle climate change and increase renewable energy use. Learn how a joint power purchase agreement offers a new way to cut value chain emissions and achieve 25% cost savings on electricity.