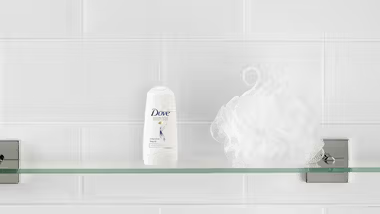
Product safety and quality
Average read time: 4 minutes
Consumers trust us to provide them with high-quality products that are safe for their intended use. We have extensive product quality and safety processes to minimise risks throughout our value chain.
Our commitment to product safety and quality
Unilever’s reputation and success is founded upon providing safe high-quality products that meet all applicable standards and regulation.
Our Product Safety & Product Quality Code Policy (PDF 122.69 KB) sets out the mandatory requirements and behaviours that we expect all our employees to demonstrate when working for Unilever.
Our Safety, Environmental & Regulatory Science (SERS) specialists work with teams across Unilever to assess the safety and environmental sustainability of our products. The Centre also evaluates the processes used to manufacture our products.
We design safety and sustainability into our products and manufacturing processes using the best science available.
Certification and capabilities
Product safety certification helps to provide assurance that our factories are operating to the highest safety standards. Our Foods and Ice Cream sites are certified to FSSC 22000 – a Global Food Safety Initiative (GFSI) benchmarked standard. Many of our Home Care, Personal Care and Beauty & Wellbeing sites are also externally certified to relevant quality and/or product safety standards. We have a programme in place to extend external certification to more sites.
We are committed to ensuring that we have the right quality capability for the business. We use our internal ‘Quality Business School’ to help our employees to build deep quality expertise so we can deliver high-quality, safe and sustainable products.
Listening to consumers, acting fast
We want to know what consumers think of our products. We’re constantly reviewing the feedback consumers kindly provide on our brands and products through a range of channels – including our own consumer care lines, as well as on social media and through product reviews on e-commerce sites.
Striving for continuous improvement
We are committed to continually improving our quality performance and our improvement programmes cover all aspects of our value chain – including suppliers, manufacturing, and route to market.
However, sometimes we fall short of our product safety and quality standards. A product might, for example, have a quality defect. Or there may be a contamination of the raw materials, or a mislabelling of ingredients. If this happens, protecting consumers’ safety is our number one priority. When necessary, we will issue a public recall of the affected products from the marketplace even if only small quantities of products are involved.
In 2022, we issued eight public recalls. Four of these were related to external manufacturers (differing causes), two were related to our own manufacturing facilities (where incorrect ingredient / pack components were used in error) and two were related to a raw material contamination issue (which also affected other consumer goods companies).
Wherever and whenever mistakes occur, we investigate them fully. We identify the root cause and share lessons learned to all relevant parties to prevent a recurrence.
For example, based on our learnings from 2022 we have strengthened our quality processes and governance for third-party manufacturers and established a proactive raw material contaminant risk management programme for our non-food portfolio, which builds on the programme we already have in place for food production.
As a result of our sustained focus on continuous improvement, we have reduced the number of marketplace incidents by more than 10% over the last five years.
10%Reduction in marketplace incidents over the last five years.
Sharing our knowledge with others
We share our safety research with the global scientific community through Unilever’s Safety and Environmental Sciences website. SERS also engages on a wide number of issues such as animal testing, plastic packaging and the ingredients we use.
We work with external organisations and authorities to develop more rigorous product vulnerability risk assessments. And we develop counter measure programmes that will help prevent malicious or economically motivated adulteration.
As well as conducting our own pioneering scientific research, we work closely with leading authorities around the world – including regulators, government scientists and academic experts. This ensures we’re always using the most up-to-date science within our safety and environmental sustainability assessments.